The lean approaches that helped Toyota improve engineering processes more than 75 years ago are still influencing productivity and efficiency in organizations today.
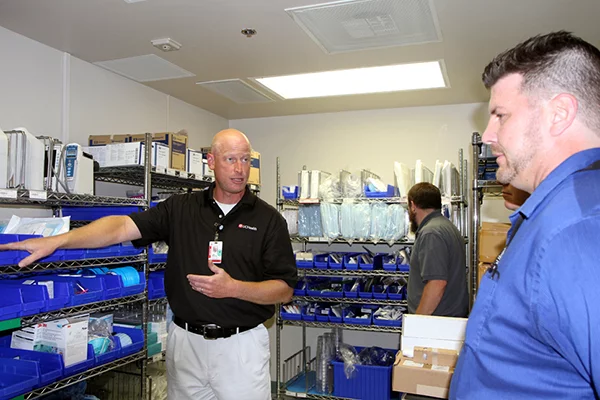
UCHealth’s Supply Chain, the Colorado-based health care system’s internal distributor of almost all its medical supplies, recently used the “kanban” inventory control approach to improve service and satisfaction — and save time.
“Our existing model just wasn’t working,” said Sean Minning, manager of Materials Management for UCHealth’s Poudre Valley Hospital and Harmony Campus in Fort Collins. “So we ran our data and came up with a methodology that we wanted to try. … The outcome was a 99 percent reduction in service calls, a 99 percent improvement in stock outcomes, an increase in nursing satisfaction and about 20 to 30 percent time savings.”
Identifying the problem
As the distributor of medical supplies for UCHealth’s northern Colorado region, with customers that include hospitals, labs, emergency rooms and urgent care centers — more than 160 supply rooms in and around Fort Collins, Loveland and Greeley — the Supply Chain team of more than 30 workers has a very important role.
“If a nurse uses it and it’s not a pharmaceutical, then we stock it, with a few exceptions,” Minning said.
As UCHealth grows, so does demand for materials. Supply Chain leaders, including Minning; Matt Putman, materials manager for Medical Center of the Rockies and Greeley Emergency and Surgery Center; and David Davis, director of materials management for UCHealth’s Purchasing in northern Colorado; realized that improvements could be made in processes.
To avoid making a large capital purchase for electronic equipment that may or may not have solved issues, the Supply Chain team opted to try a lean practice. Their goal was to not only improve product distribution without capital purchases but also increase nursing satisfaction.
“This change wasn’t just about the customer — it was about everyone,” Minning said. “It was about both our customers and Supply Chain being able to do something that makes both of us more efficient.”
To test their new methodology, the team implemented the new practice in the GI labs at both PVH and MCR.
The labs presented two major challenges: limited space to house supplies and supplies that don’t come out of UCHealth’s supply warehouse but rather are special-order products from multiple vendors. The result: The unit ran out of stock of some items, affecting customer satisfaction and adding legwork to the Supply Chain’s employees who had to make regular service trips to the labs to restock items.
“At one point I was going there a minimum of four times a week on recovery calls,” Mining said about PVH’s GI lab.
The solution
The old system was in place because, well, it was just the way things were done, Minning said. The old way of stocking supply rooms meant that several different items could be in one bin, and Supply Chain employees had to count each item to determine whether more products needed to be ordered.
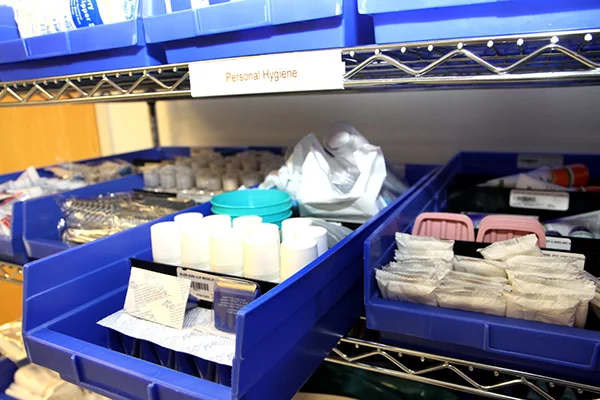
Although each bin held multiple items, the system actually took more space because there needed to be room above each bin for the customer and Supply Chain employee to peer inside and see which products it held.
The new system uses a high-density storage strategy. By organizing a product in a linear fashion — the product in the front of the bin to be used first and the row behind being the emergency stock — shelving can be vertically closer because the product is always front facing. And if the front part of the bin is empty, the Supply Chain employee knows to reorder. It’s all or nothing — no need to count individual stock. This cuts ordering and stocking time by a minimum of 25 percent, Minning said.
Those extra minutes are now used to do extra cleaning and rotation, he added.
The new design also lends itself to a more efficient rotation system. Once the new stock has arrived and is ready to be put on the shelves, the emergency stock is moved forward and a new emergency allotment placed in the back.
“This simple and inexpensive fit-to-space kanban solution removes nursing from the task of managing inventory and ensures that supplies are always there, eliminating both stock-outs and the resulting hoarding that often takes place,” Davis said.
For the process to be successful, it’s important that both the hospital unit and Supply Chain do their parts, said Brenda Lynch, nurse manager for PVH’s GI Lab. She said that her staff has committed to keeping maximum supply levels in procedure rooms instead of hoarding products in fear of not having enough. Hoarding, Lynch said, can lead to increased costs due to products expiring and having to be discarded.
This commitment resulted in adequate inventory and significant cost-savings. But, she said, the new system has helped to improve the department’s culture. Staff are no longer stressed about not having adequate supplies on hand, Lynch said.
“It’s huge for a department’s culture when you have everything you need at your fingertips,” she added. In addition, since the clinical staff was involved in the reorganization process, they know where supplies are and they are confident they will be there when they need them.
Sharing the success
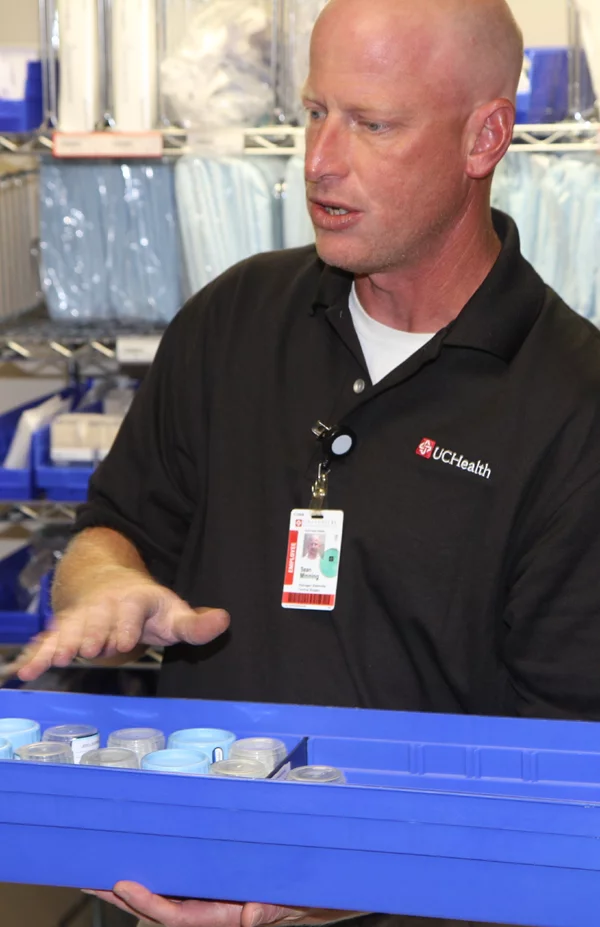
The transition to the new methodology will continue to be implemented throughout PVH and MCR in the coming year, Davis said. As UCHealth constructs and opens new hospitals and remodeled units, the system will be incorporated into their designs.
Such was the case for PVH’s remodeled Neonatal Intensive Care Unit that opened in May. It was designed with two supply rooms at each end of the unit, both having the new stock system.
“It is well organized and labeled nicely,” said NICU nursing assistant Dawnielle Edmonds. “It took a bit of getting used to, but you can see the items better, it looks better and there seems to be more room. And our everyday-use items are on both sides of the unit, which saves us steps.”
The new stocking system also will be incorporated into UCHealth’s new hospitals coming to the Longmont, Greeley and Highland’s Ranch areas.
Materials Management departments at University of Colorado Hospital and Memorial Hospital also are considering how the new system may be beneficial. Though both regions have slightly different ordering systems and supply room configurations, leaders from those regions visited PVH on July 14 to see if they could take anything away from the changes Supply Chain has made.
“I’m gaining some organizational ideas that we might be able to blend into what we are doing,” said David Rowley, materials manager at UCH. “We have limitations with the inventory management system we use, but there may be some future ideas.”